The following is part two of a series of 3 blogs that will go through a white paper written by New Era Converting Machinery’s Bob Pasquale. The white paper is titled “Design Considerations in Unwind Tension Control Systems.”
Part 1 offered an overview of the entire paper and what to expect in coming blogs. Part 2 will go through sizing a braking system and various types of braking systems on the market. Part 3 will wrap the series up with types of braking systems controls and offer a brief conclusion.
—–
Part 2: Sizing and Types of Braking Systems
SIZING OF THE BRAKING SYSTEM:
As indicated above, the braking system is designed to develop the required force to provide the proper web tension. The braking system’s force must stay in balance with the web force in order to maintain web tension. This concept is of particular importance when you consider that the diameter of the roll of material continues to decrease as the material is unwound. The forces between the braking system and the roll of material are balanced through torque, which is defined as:
Torque = force X radius
Therefore, as the size of the unwinding roll decreases, so to must the force of the braking system in order to maintain a constant force (tension) on the web.
The properly designed braking system must be able to deliver the required force both at the full roll, when the radius and therefore the required force is biggest, as well as at the core, when the radius and therefore the required force is smallest. Additionally, if multiple materials, thicknesses and web widths are to be unwound, then the braking system must be able to compensate in order to deliver the required forces throughout the range of products.
The generation of force required to provide the web tension results in the production of power, measured in horsepower. The braking system must be appropriately sized to allow for this energy to be handled. The formula for calculating the braking system’s horsepower requirements vary depending on the type of braking system used and are provided below.
In addition to these two primary calculations, several other design criteria need to be considered including the braking systems ability to dissipate the generated heat at the operating speed(s), the systems ability to rapidly stop the unwind roll during emergency stopping conditions and the systems reflected inertia.
TYPES OF BRAKING SYSTEMS:
Through the years many different systems have been used for unwind braking. In the past it was common to see braking systems as simple as a wood vise clamped to the unwind roll’s shaft and tightened/loosened to adjust the tension or leather straps draped over the unwinding roll’s core or shaft from which weights were hung. Today’s unwinds are typically provided with either brakes or motor/drives to generate the required torque.
A system based on using a brake is one where a device imparts a drag force on the unwind shaft to allow the web tension force to be developed. Based on this explanation the previously described vise and leather strap meet the definition. However, for the purpose of this presentation we will consider brakes that are either pneumatic or electric in nature. In these cases either a pneumatic pressure or electrical power is applied to the brake assembly to generate the required torque. The resultant braking force is regulated by adjusting the pneumatic pressure or electric power which varies the drag that is applied to the unwind roll and therefore varies the tension.
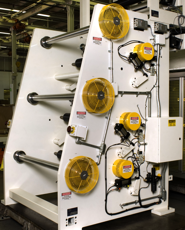
When sizing a brake, in addition to calculating the torque requirements, one must also calculate the brakes horsepower (HP). This is calculated using the following formula:
HP = [Web Tension (pounds) X Web Speed (feet per minute)]/33,000
As a side note, the above formula indicates the Web Tension in pounds. This represents the total force on the web. Should the above table(s) be used to calculate the web tension then the following formulas apply:
For Films:
Web Tension = tension level (lb/inch/mil) X web width(inches) X web thickness(mils)
(1 mil = 0.001”)
For Papers and Paperboard:
Web Tension = tension level (lb/inch) X web width (inches)
In addition to sizing the brake for the torque and horsepower required, other factors need to be considered, such as the brakes ability to dissipate the heat that is generated and whether the brake needs to be air cooled or water cooled, etc.
Brakes do offer certain advantages over motor/drive systems. They are typically less costly to purchase, install and operate, are easy to operate and require minimal maintenance. Pneumatic brakes are excellent for use in hazardous rated electrical areas (since they are non-sparking) as long as the heat they generate remains below the required levels.
However, there are also disadvantages to using a brake. They can be limited in their total tension range. They may not work well at very low tensions since the lowest drag of the brake may exceed the minimum tension requirements. Additionally, for certain low tension applications the force required to rotate the unwind roll may exceed the tension force; in this case, the use of a brake is precluded. Brakes often do not work well with damaged rolls where the forces required to overcome the damage may exceed the tension force. Brakes often have problems during the acceleration phase of operation, where the forces to accelerate the roll can exceed the web tension forces. Finally, brakes do not lend themselves well to applications where the roll of material needs to be accelerated prior to unwinding, such as in automatic splicing systems.
Based on the disadvantages outlined above, many of today’s unwinds are provided with motors/drives. In this case the motor is excited (powered) by an electronic drive to act as a generator, requiring torque to rotate its shaft. By coupling the motor’s shaft to the unwind roll, the torque required to rotate the shaft is used to provide the force needed to generate the web tension. As the motor’s excitation current is varied so is the torque required to turn the motor’s shaft, allowing the web tension to be varied.
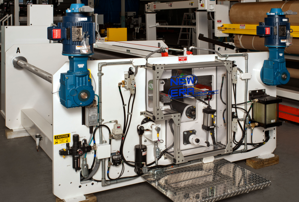
When sizing the motor/drive for an unwind, one needs to calculate the horsepower (HP) requirements for the system. The formula for this calculation is as follows:
HP = ( [Web Tension X Web Speed] /33,000 ) X ( [Max. Unwind Roll Diam.] / [Min. Core Outside Diam.] )
With:
Web Tension in pounds
Web Speed in feet per minute
Maximum Unwind Roll Diameter in inches
Minimum Core Outside Diameter in inches
The same notes that applied to the brake formula regarding the Web Tension still apply here.
Though motor/drive based braking systems are typically more expensive to purchase and install, they do offer several advantages over systems that feature brakes. They work well in low tension applications when unwinding requires a motor to power the roll in order to turn it without exceeding the minimum tension. Likewise, motor/drive controlled unwinds are beneficial during roll acceleration, when power may need to be provided to the roll of material to get it up to speed without exceeding the required tension forces. They are also very good for handling damaged rolls, allowing the force to the roll to be switched from braking to motoring, as needed to unwind the material. Another area where motor/drive controlled unwinds are beneficial is when a roll of material needs to be brought up to speed before the process of material unwinding begins, as is typical in automatic splicing; the same system can be used to accelerate the roll and then provide braking once the unwind splice has occurred.
As with any braking system, the force that is supplied to provide the web tension results in the generation of energy which needs to be dissipated by the system. For a brake based system the energy is dissipated in the form of heat. An advantage of a motor/drive system is that this energy can be removed in the form of electrical power and returned to the plant.
A motor/drive based braking system is not well suited for very slow speed applications. In this case a large mechanical speed reduction is required between the motor and the unwind roll, potentially resulting in large power loses in the system. The large transmission ratios also result in high reflected inertias which makes it very difficult to precisely control the forces at the unwinding roll.
###
*Check back soon for the third and final blog in the series, or go back and read Part 1!*