The following is the first part in a series of 4 blogs that will go through a white paper written by New Era Converting Machinery’s Bob Pasquale. The white paper is titled “Lamination System Application and Design Considerations.”
Part 1 will offer an abstract and introduction to the blog series, as well as an overview of Wet Bond Lamination. Part 2 will go through Dry Bond Lamination and Thermal Lamination. Part 3 will discuss a few design considerations, including Roll Design, Nip Pressure Control, and Gap Control. Part 4 will wrap the series up, finishing with design considerations including the Roll Drive, Alignment, Web Handling, and Guarding and then offer a brief Conclusion.
—–
OVERVIEW:
This presentation covers several different methods that exist for laminating multiple webs as well as how the process requirements determine which method is most suitable. It also covers several areas of consideration for the proper design of the laminating system including pressure and gap control of the lamination nip, construction of the laminating rolls, temperature control of the laminating rolls, driving of the laminating rolls, and web handling into and out of the laminating section.
INTRODUCTION:
Lamination, which is the process of combining multiple webs to form a new, single, multilayer web, is performed for many reasons using a wide variety of webs to form a multitude of products. These reasons can be divided into several categories including:
- Mechanical – here the layers are combined to improve the mechanical properties of a web; examples of this are laminates designed to increase the tensile strength, add a wear resistant layer or add a protective layer
- Chemical – here the layers are combined to improve the chemical properties of a web; examples of this are laminates combined to reduce the web’s vapor, gas or moisture transmission rates
- Decorative – here the layers are combined to improve the appearance of a web; examples of this are adding a film to change the surface appearance of the web or adding a printed film to the web
The type of lamination system that is used to combine the webs depends on several factors including the web materials that are being laminated, the method/adhesive being used to join the webs, and the desired properties that are to be obtained by the product.
Regardless of the lamination system that is used, in all cases the webs are combined at a lamination nip. This nip is typically made up of two rolls that are either pressing together under a controlled pressure or have a controlled gap between them. Typically one of the rolls features a hard surface such as chrome plated steel, with the other roll featuring a resilient surface such as rubber.
For purposes of this paper we will be covering all of the major types of laminating systems with the exception of extrusion lamination which, due to the differences it has with the methods discussed here, can and should be covered in a separate paper.
TYPES OF LAMINATING SYSTEMS:
The method by which webs are laminated together can be divided into three major categories which are typically defined as Wet Bond, Dry Bond, and Fusion lamination. The physical properties and characteristics of the materials that are to be combined determine which of the above methods is used.
WET BOND LAMINATION:
In Wet Bond lamination a coating is applied to one or more of the webs which are then combined while the coating is still in a liquid form. This type of lamination can take one of several different forms.
If the adhesive includes a water or solvent carrier, a drying process is typically required to remove the water or solvent with it passing through one or both of the webs. In this case at least one of the webs needs to be permeable/porous, with the adhesive typically being applied to the non-porous web so that it stays on the surface. Once combined, the laminated product typically either passes through a dryer (See Figure 1) or about a heated drum (with the permeable web out) to remove the moisture. In certain cases, particularly where light water based adhesives are used in conjunction with an absorbent web, drying may not be required to remove the water.
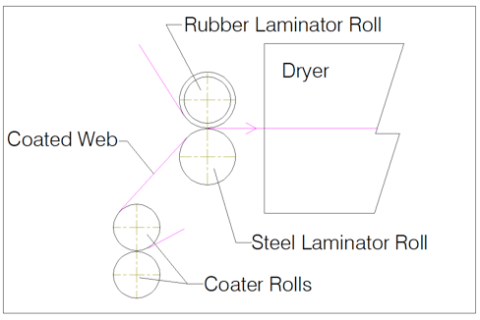
Another form of wet bond lamination is one in which a 100% solid curable or cross linking adhesive is applied to one or both of the webs. Once the webs are combined, the curing/cross linking is performed through the web(s) with a system such as a U.V. unit. In this case neither web needs to be permeable since the 100% solid coating has no water or solvent that needs to be removed.
An additional form of wet lamination is one in which waxes, paraffins, or similar thermoplastic adhesives are used. Here the coatings are heated to their liquid form and applied to one or both of the webs. Once these webs are combined, the coating is cooled back to its solid state by passing the laminated product about a cooling roll(s) (See Figure 2), through a water bath or through a cooling chamber. Like the curable/cross linked adhesives, since the coating is 100% solid, neither web needs to be permeable since no water or solvent needs to be removed.
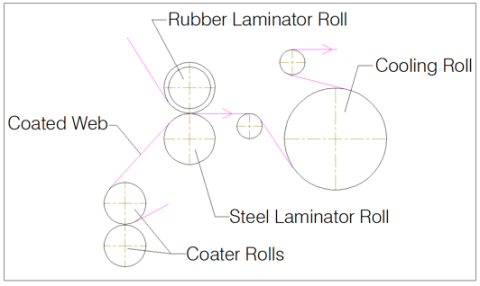
The lamination nip on a wet bond laminator is typically either run at a low pressure and/or with a gap between the rolls. This is a critical requirement since the adhesive between the layers of web is still in a liquid form. Too much pressure can result in the adhesive being squeezed into the porous web or out from between the webs, resulting in poor bonding of the layers.
It is desirable to have the lamination point as near to the coating application point as possible. This will prevent the premature flashing of the solvent or water, as well as the absorption of the coating into the web (if it is porous). Once the webs are combined, it is important that they are dried (if using a water or solvent based adhesive), cured/cross linked (if using a 100% solid curable or cross linked coating), or cooled (if using thermoplastic adhesives) as soon as possible since the adhesive doesn’t develop its full strength to hold the webs together until this happens.
###*That concludes part 1 of our 4 part blog series, “Lamination System Application and Design Considerations” – check back soon for part 2!*