There are many methods currently available for online measurement of coating thickness. A major benefit of these measurement systems is the ability to use the information to control the coating application in order to obtain a targeted laydown. This control can be performed in several ways, including:
- adjusting the speed of the coating application roll(s)
- adjusting the speed of the coating delivery pump
- adjusting the speed of the web processing line
- adjusting the coating gap
- adjusting a combination of the above
Quite often the coating method dictates which of the above methods is most desirable.
We will look at each of these methods, discussing how they are used to control the application rate, what types of coaters they are used with and how the thickness measurement system can be interfaced with them.
Adjusting the Speed of the Coating Application Roll(s)
There are several coating methods where the coating is transferred to the web using an applicator roll running in either the same or opposite direction of the web. In either method, adjusting the speed of the applicator roll directly affects the amount of coating that is applied. Therefore, in these methods, the thickness measuring system’s information is used to adjust the speed of the applicator roll to control the coating transfer.
Examples of these coating methods include kiss coating (Photo 1) and offset gravure coating (Photo 2).
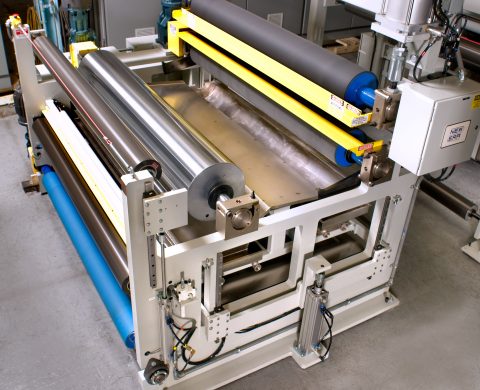
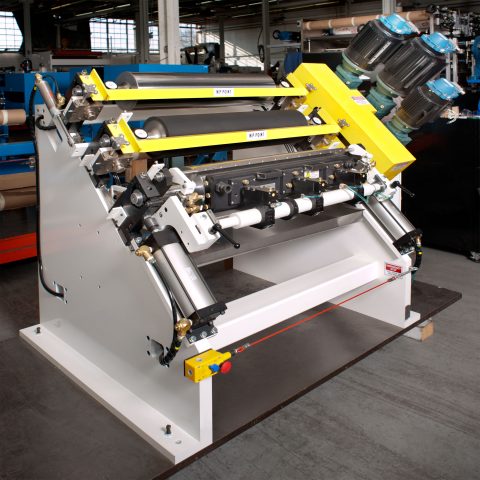
The ease with which today’s drive and control systems can accurately control a motor’s speed allows this method to implement highly accurate adjustments to the coating rate. Interfacing of the thickness gauge system with the drive system allows for fully automatic closed loop control of the application rate.
Adjusting the Speed of the Coating Delivery Pump
Certain coating methods apply a pre-metered amount of coating to the web through the use of a precision metering pump. In these cases the information from the thickness measuring system is used to speed up or slow down the pump in order to affect the amount of coating delivered to the web.
Typical examples of this type of coater are slot die coaters (Photo 3) and spray coaters (Photo 4).
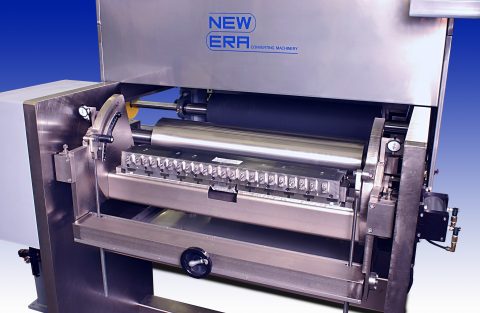
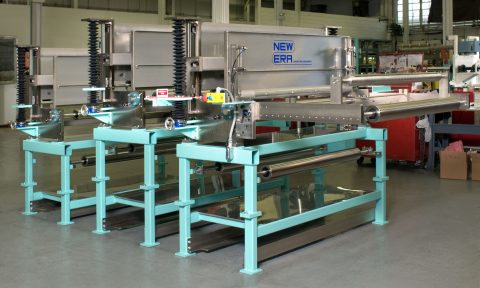
As previously discussed for the applicator rolls, the ability to control the motor’s and therefore the pump’s speed on a finite basis allows for making precise adjustments to the coating laydown rate as well as automatically controlling the thickness via closed loop control.Adjusting the Speed of the Web Processing Line
There are certain cases in which a pre-metered amount of coating is delivered to the web but it is not practical to change the rate at which the coating is being delivered to the process. This particularly applies to processes where the mixing or production of the coating is critical. In these the information from the thickness measuring system is used to speed up or slow down the web speed in order to affect the amount of coating delivered to it.
A typical example of this is extrusion coating.
Again, as in the previous two example, today’s drive and control systems can accurately control the speed of the system’s motors, allowing for highly accurate adjustments to the coating rate. Interfacing of the thickness gauge system with the drive system allows for fully automatic closed loop control of the application rate.
Adjusting the Coating Gap
Several coating methods rely on a gap to control/meter the amount of coating applied to the substrate. This gap can take several forms including between two rolls or a roll and another metering device such as a knife blade. In certain cases the gap between the two members is used to pre-meter the coating prior to it being introduced to the web while in other cases the coating is introduced to the web at the gap, resulting in the total thickness of the coating plus the web being metered. In these types of coaters, adjusting the gap between the rolls or roll and knife changes the amount of coating that is applied. Therefore, in a closed loop system the information from the thickness measuring system is used to open or close the gap in order to affect the amount of coating delivered to the web.
Examples of this type of coater are knife over roll (Photo 5) and between the roll coaters (Photo 6).
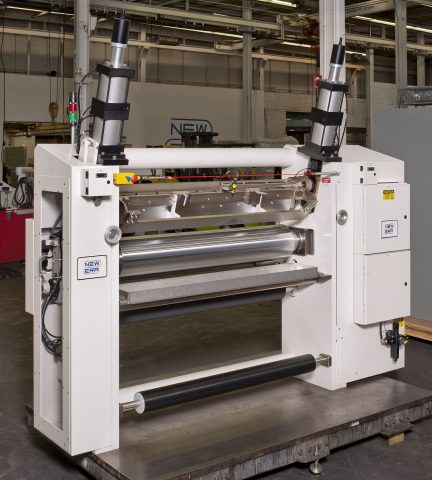
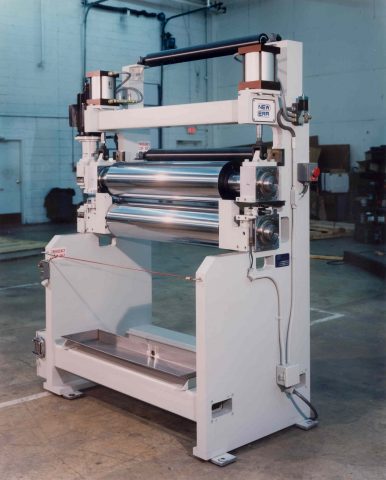
In these types of coaters adjustable devices typically allow the gap to be varied. The information from a thickness measuring system can be used for closed loop control of these devices and therefore the gap through the use of positon controlled motors that are tied to the devices as well as position feedback devices that monitor the gap. Such a system is shown below (Photo 7).
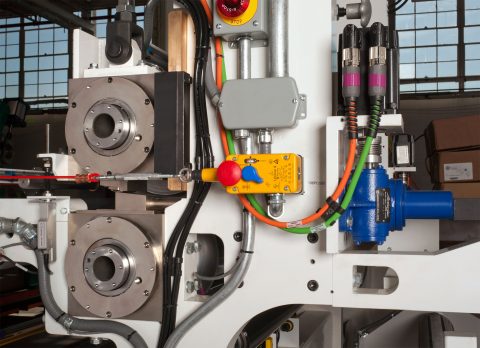
Adjusting a Combination of the Above
In certain coating applications such as a reverse roll coater a combination of speed and gap control is used to control the amount of coating being applied to the web.
In this case the speed of the applicator roll is used for minor changes in the coating rate while larger changes are handled through adjustments to the gap between the rolls. In applications such as these a combination of the previously described methods of control is used to control the coating application rate. Such a system is shown below (Photo 8).
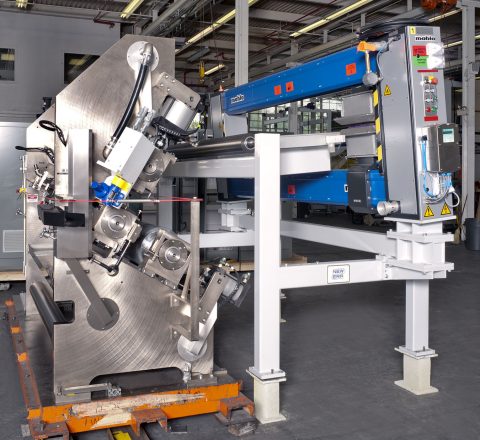
As demonstrated above, there are many different systems available that allow for the use of a thickness measurement system to control the application of a coating, with the type of coater dictating which method is most suited.