A New Era automatic turret winder, with a 102″ roll face, automatic roll transfers, edge trim slitting and automatic tension control is available for sale immediately. The unit can be customized with a drive system of the end users preference. The original unit was designed for use with 6″ cores (shaft-less chucking) and roll diameters up to 48″ with a maximum roll weight of 4400 lbs. A more detailed description of the unit is shown below:
SLITTER:
- Type – Shear slitting edge trim section. System allows for edge trim of up to 10” per side. Trim removal is not included.
- Construction – Heavy duty steel fabricated side frames with tubular steel stretchers. Designed for direct floor mounting.
- Shear Knives – Two Tidland Class II Performance Series Auto shear Swing Knife holders with manual mount.
- Support – One Tidland Edge-trim support beam with linear bearing rail.
- Anvil – Two Tidland Knife rings, D-2 steel, class 2.
- Controls – The following machine mounted devices are provided:
- Guard interlock switches
- Pneumatic feed complete with lockout valve, filter and regulator
- Emergency Stop rope pull cord
TURRET WINDER WITH AUTOMATIC TRANSFER:
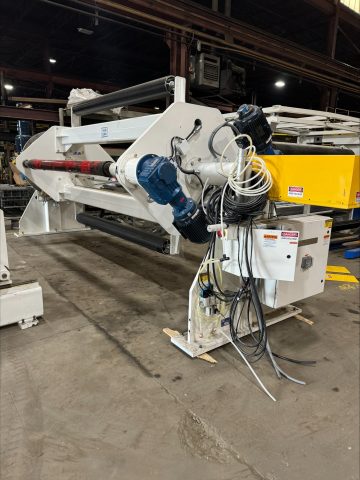
- Type ‑ Two position indexing turret with single direction over mode automatic transfer.
- Construction ‑ The turret is constructed of heavy duty pedestals with steel tube stretchers for rigidity. The equipment is designed for direct floor mounting.
- Turret Assembly ‑ Heavy wall tubular steel cross shaft with precision bored flanged heads. The cross shaft is pillow block mounted on drive side with hollow shaft Cone Drive worm reducer on operating side. The reducer has a variable speed A.C. motor with brake to prevent turret drift. An air-over-hydraulic caliper disc brake is also provided to lock the turret into position.
- Turret Arms ‑ Fabricated steel construction mounted in fixed position on turret cross shafts. NOTE: This will allow shafted chucking of 6” I.D. cores.
- Chucking & A.C. Motors ‑ Drive side turret arm has spindle assemblies with mechanical drive transmission products to individual turret arm mounted A.C. motors for winder web tension. Operating side and Drive side spindle assemblies are provided with chucks to suit 6″ diameter pneumatic shafts.
- Tension Control ‑ A pneumatically loaded pendulum type dancer roll with diaphragm air cylinders and lead‑in and lead‑out idlers, controls a two‑motor A.C. drive; one motor to each spindle. This assembly is located in the moving carriage (transfer system).
- Single Direction Flying Transfer System – The tension control system and flying transfer system are mounted on a motorized carriage, which moves on linear tracks and ball bushings. The system provides fully automatic core start at full line speed. The automatic transfer sequence is as follows:
- While spindle “A” is winding, the operator loads a new core onto spindle “B” and applies double side adhesive tape to the core.
- Through a signal initiated from the first pre-set position of the web length counter or the product roll diameter monitor or by operator initiation, the turret is indexed to position the new core into the transfer position.
- The flying transfer carriage then travels into the transfer position and the new core is accelerated to matched speed with the web.
- When the required web length or wound roll diameter is reached, a signal is given to fire the bump roll in sequence with the cut-off knife and the leading edge is automatically started on the core.
- The bump roll and cut-off knife are retracted.
Note: A manual sequence is also provided with an auto/manual selector switch to permit manual sequencing to be carried out. The manual mode will override the footage or diameter presets to commence the transfer sequence.
- Pack / Gap Winding System – The pack roll system consists of a pneumatically operated, rubber covered roll mounted on an AC Vector motor-driven carriage assembly. The pack roll maintains contact with the winding bundle from time of transfer to the new core until indexing begins. The pack roll and is actuated by pneumatic cylinders for precise movement. Loading is thru an E/P transducer. The control system senses movement of the pack roll cylinders and automatically adjusts the driven carriage’s position to maintain constant pressure. In addition, the controls and feedback devices enable “gap” winding, (adjustable gap settings are entered at the local HMI).
- Guiding – None Provided.
Contact us to find out more https://neweraconverting.com/contact-us
To see videos of other New Era Automatic transfer winding equipment, click here