The following is the first part in a series of 5 blogs that will go through a presentation given by New Era Converting Machinery’s Bob Pasquale at 2018 AIMCAL R2R Europe Conference. The presentation is titled “Selecting an Unwind and Unwind Splicer System.”
Part 1 will offer an overview and introduction to the blog series, as well as the holding of the roll while unwinding. Part 2 will discuss tension control of the unwinding material. Part 3 will go through the guiding of the web as it exits the unwind and how the expiring roll’s web will be spliced to the beginning of the new roll’s web. Part 4 will continue with a consideration of how the expiring roll’s web will be cut and the number of unwind positions. Part 5 will wrap the series up, finishing with a comparison of roll to roll versus continuous unwinding, and then offer a brief Conclusion.
OVERVIEW
In this presentation, we will cover the factors that need to be considered when selecting an Unwind and Unwind Splicing System. We will cover several areas that need to be determined in the design of the unwind system including:
- Holding of the web rolls when unwinding
- Tension control of the unwinding material
- Guiding of the web as it exits the unwind
- How the end of the expiring roll’s web will be spliced to the beginning of the new roll’s web
- How the expiring roll’s web will be cut
- Number of unwind positions
- Roll to Roll versus Continuous Unwinding
Several process related factors influence the choices associated with each of these areas will also be discussed in this presentation, including:
- Speed of the process
- Web tension requirements
- Web width
- Weight and diameter of the web rolls
- Type of web materials
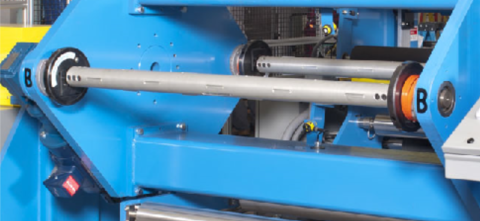
For each of the previously outlined features we will discuss how the design choices impact such factors as:
- Technical advantages and disadvantages
- Cost implication/impact
- Safety
For purposes of this presentation we will be discussing center unwinds, where the material roll is supported through a core located in the middle of the roll.
HOLDING OF WEB ROLLS WHEN UNWINDING
The biggest consideration when discussing how to hold a roll of web in an unwind is whether a shaft is to be used.
Shafted Unwind:
An unwind where a bar is placed inside the web roll’s core to support it and interface it with the unwind. This bar is typically locked to the core to prevent slippage between the two and features ends designed to interface with unwind mounted holders, allowing the web roll to be supported. These holders allow for the rotation of the roll of material so the web can be paid out.
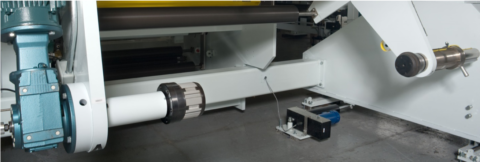
Advantages:
- Lower equipment cost
- Lower maintenance
- Smaller equipment footprint
Disadvantages:
- Requires the need to handle shafts – particularly an issue on wider webs and larger diameter cores, where the size and weight of the shafts becomes a logistics, ergonomics and safety concern
Shaft-less Unwind:
An unwind where the web roll is held by unwind mounted supports that are inserted into the ends of the web roll’s cores and are designed to prevent slip between them and the core.
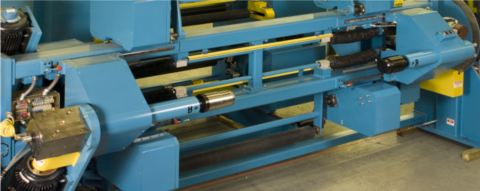
Advantages:
- Eliminates the need for handling of shafts
Disadvantages:
- More costly than a shafted unwind
- Larger equipment footprint
- Higher maintenance
###
*That concludes part 1 of our 5 part blog series, “Selecting an Unwind and Unwind Splicer System” – click here for part 2!