The following is the third part in a series of 5 blogs that will go through a presentation given by New Era Converting Machinery’s Bob Pasquale at 2018 AIMCAL R2R Europe Conference. The presentation is titled “Selecting an Unwind and Unwind Splicer System.”
Part 1 offered an overview and introduction to the blog series, as well as the holding of the roll while unwinding. Part 2 discussed tension control of the unwinding material. Part 3 will go through the guiding of the web as it exits the unwind and how the expiring roll’s web will be spliced to the beginning of the new roll’s web. Part 4 will continue with a consideration of how the expiring roll’s web will be cut and the number of unwind positions. Part 5 will wrap the series up, finishing with a comparison of roll to roll versus continuous unwinding, and then offer a brief Conclusion.
GUIDING OF THE WEB AS IT EXITS THE UNWIND
An important consideration is the need to guide the web as it exits the unwind. Though some unwinds are provided without the means of adjusting the web’s cross machine position, most include some form of adjustment, either as a manual or automatic system.
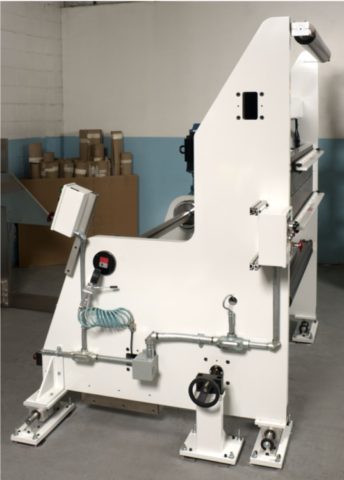
Manual System
A manual system is where either the roll of web or entire unwind is manually shifted in the cross machine direction.
Advantages:
- Low cost
- Minimal maintenance
Disadvantages:
- No method for precision adjustment of the web location
- No method for continuous adjustment
Automatic System
An automatic system is one where the web location is continuously sensed and automatically corrected.
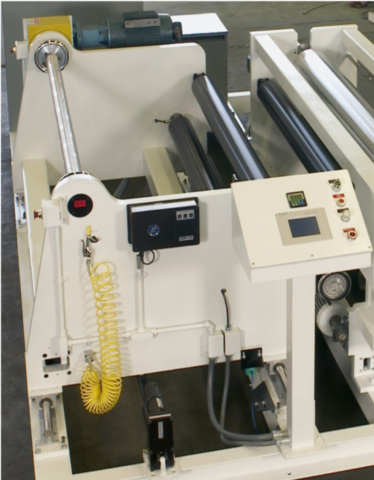
This can be edge, line or center guiding and uses an actuating device to adjust the web’s position by moving the unwinding roll or entire unwind in the cross machine direction, or by pivoting a roll or pair of rolls that the web passes over upon exiting the unwind to steer it to the desired position.
Advantages:
- The web is automatically guided to a precise location
- Guiding of the web is continuous
Disadvantages:
- Higher cost of equipment
- Higher maintenance
SPLICING THE EXPIRING ROLL ONTO THE NEW ROLL’S WEB
The method of joining the end of the expiring roll’s web to the beginning of the new roll’s web is typically dependent on:
- The web materials
- The process that the web is entering
To be considered are:
- The method of joining the webs
- The type of splice to be formed
The Method of Joining the Webs
There are several methods available to join the webs together such as:
- Pressure sensitive tapes or adhesives
- Heat and pressure activated tapes or adhesives
- Sewn splices
- Welded splices
The selection of the method of joining the webs is typically
dependent on:
- The web material – what methods of joining the webs works with the particular web material
- The process – what methods of joining the webs allows for the splice to survive the process conditions such as:
- Tension
- Moisture
- Heat
The Type of Splice to Be Formed
The most common types of splices are:
- Lap splice – the expiring web’s end overlapping the new web’s leading edge; this is the easiest splice to perform
- Butt splice – the expiring web’s end butts up against the new web’s leading edge; this splice is more difficult to form, requiring more work and time to prepare/perform
The selection of the type of splice to be formed is typically dependent on:
- The web material – what type of splice works with the particular web material; an example is a web with a liner that will later be peeled on a continuous basis, requiring a two sided butt splice
The selection of the type of splice to be formed is typically dependent on:
- The process – what type of splice allows for the web to make it through the process; examples of this are conditions such as:
- the double thickness of web from a lap splice will not make it through the machine
- a hanging tail from a lap splice may result in problems
The design of the unwind should allow for the required splice to be formed.
This could range from no hardware required for the operator to form a manual zero speed splice on the roll of web to the inclusion of a special splice assembly like shown below:
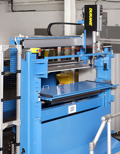
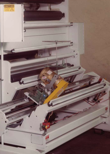
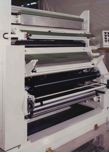
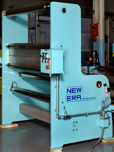
###
*That concludes part 3 of our 5 part blog series, “Selecting an Unwind and Unwind Splicer System” – continue with part 4 here, or go back and read part 1 here, or part 2 here!